Selected Technique:
Controlled Modulus Columns
Project:
3300 Columns
A 4-level warehouse located within the South Dufferin Industrial park in Calgary was approved to support a supply chain facility. Ledcor was contracted to design and construct the warehouse, which included a 65,000m2 warehouse, large docking areas, heavy parking, light parking, and few access roads. The engineer recommended stone columns as a ground improvement solution, but Menard Canada’s Design and build team proposed Controlled Modulus Columns (CMCs) to achieve the required bearing capacity, reducing the post-construction settlement. In addition, CMCs are cost-effective, swiftly operated with little vibrations, and generate nominal/no spoil during execution.
Ground Conditions
The general subsurface stratigraphy consists of:
- Structural Clay Fill in the top 0.5 to 2.0m;
- Loose Clay for the next 4m;
- Firm Clay Till for the next 2m;
- Siltstone and Shale made up the bedrock beneath.
The groundwater table is at approximately 3m.
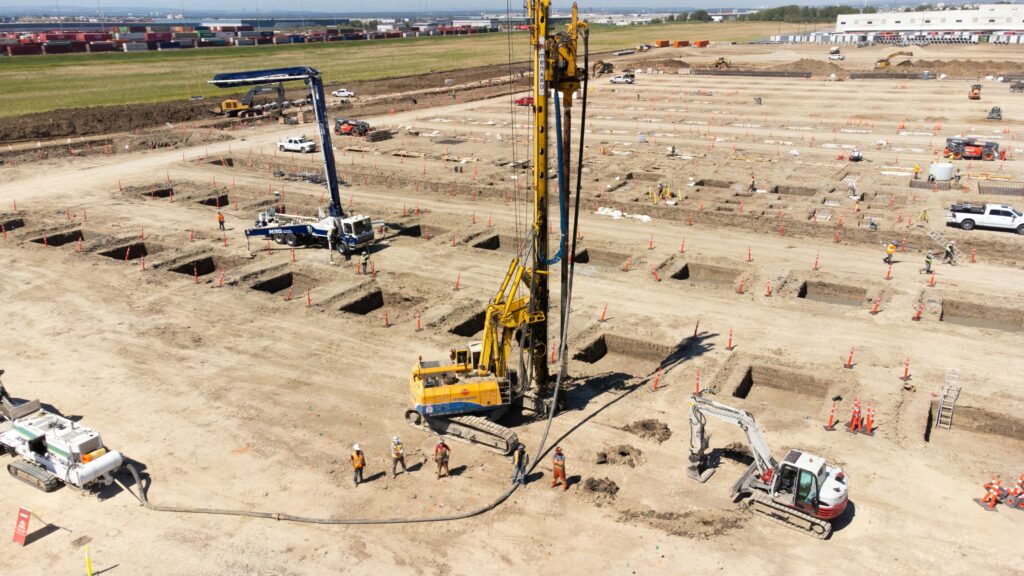
YYC4 Project Maverick – Warehouse – Calgary, Alberta
Menard Canada Solution
Menard Canada performed five static load tests on isolated CMCs to verify the design and performance of this solution. The resulting settlement was less than 1/4th of the specified requirement, proving an effective solution. CMCs are robust and inexpensive compared to other ground improvement techniques.